Dry leveling floors are used in the case, when the entire scope of work to be done in the shortest possible time. Here we do not need to spend time preparing the mixture, and after the execution of works - to dry for a long time. Once I managed to level the floor dry screed, possible to start laying a floor covering. But it is very important to know what does it do and what is required to purchase. Composition of the screed for the floor will depend on the specific type of work and technology. Full combination of components allows to get a really high quality results.
Composition of the screed, depending on the species
If we take into account a brand dry screed, how Knauf, their manufacturer highlights 4 basic types of ties:
- Alpha. They are used in the presence of a base slab with a smooth. This is practically the easiest option, which includes the use of the edge band, for floor leveling layer, polyethylene film and screed, formed from sheets of GOLS.
- Beta. They consist of materials, can significantly improve sound and heat insulation qualities. May be applicable also porous, sponge materials. In any case, here also has a flat base surface, which contributes to the speedy execution of works. The alignment layer is not used, but instead carried filling the dry mixture, that is selected for this option,.
- Vega. Besides leveling layer, not skipped and insulation layer. To this dry mixture was used to screed, which will depend on the specific form of the future "finish" sex. As the insulation layer may be applied rockwool, It is a porous, fibrous material.
- Gamma - this is the most difficult type of floor unit dry mixes. There must always be available to be layers of the embodiments presented above: sound insulation layer and, alignment layer and the porous spongy material,. Besides the main layer of sheet material, and compensation should be, located below the substrate. Moreover, these boards for dry screed must comply with the declared quality.
Types of dry screed
As we can see, they are divided into these groups, depending on the purpose and the process of production and installation work. A specific method of dry screed selected by the customer and must from the outset to pass successively exposed stages. Only in this case,, compliance with technology, "Rough" sex option will smooth over the entire surface.
required tools
To perform a full range of activities, should develop a tool to tie their own hands dry. The whole set is not always useful, but more than it will not be exact. To establish a specific list should be approached individually, depending on the situation on work. Do not be amiss to attract and mate, to which even the plates for dry floor screed can be moved much easier and more cost-effectively powers. Among the tools included:
- Pencil in conjunction with a tape measure. They can be used to make measurements, make notes in the right places.
- Since the sheet material is necessary in any case to cut down to size, it is useful or conventional jigsaw blade, specially designed to undercut sheets GVL.
- Regarding the sheet material, We have all joints connected to each other with screws. In this case, we will approach screwdriver or a regular screwdriver.
Subtleties fixing floor elements Everything will depend on, whether there is a rush, and how should effectively carry out all kinds of work. In any case, laying floating floors must be performed qualitatively.
- A narrow trowel and usually need to, to dry mortar screed was distributed evenly throughout the space plane.
- As lighthouses commonly used metal profile PN 27/28. there is, of course, and alternatives, which will differ in their properties and qualities.
The paint brush and can act as a tool. But it can hardly be attributed to a number of basic. It is useful in the event that, when it will be necessary to sweep the dry mixture from place sheet material prior to the direct application of glue joints.
You can of course list and a number of other accompanying instruments. But everything will depend on the nature of work at a particular stage, as well as the preferences of the artist.
The material for
In addition to the tools themselves have to worry about purchasing and material to carry out all the work. You can make purchases in separate batches, and you can buy immediately a full range of materials, what is the most optimal one for. Here exactly you should not worry about, that product quality is at the highest level. For the device, we need a floating floor:
- sheets GVL, which are made of gipsovolokna. The most trusted manufacturers - a German company Knauf. Reduced size makes them 120*60 cm. This option is suitable for performing the independent exercise of all kinds of work. They are presented in the form of two plates, interconnected. When this plate are offset relative to each other, To get rebate. At the time of the acquisition is not superfluous to buy interest 10 plates, than necessary for the calculations. This allows problem-free cutting them for a full docking.
- can be performed dry screed sand of expanded clay
or a completely different material selected, which is in the range presented in the building products market. The most important thing, that there was a corresponding fraction of, not exceeding 5 mm.
- Consumables, which include a polyethylene film, screws, glue, Damper tape, etc.. Flow is approximately screws 12 pieces per m2.
- Putty and primer. This is useful in case, if the corresponding field is performed for a specific coating.
The choice of filling
such material, as a mixture of dry floor base unit, given essential. It comes from the fact, that particular room, and floor covering should be combined with fully used backfilling. Most often sold dry screed in bags. All will depend on the desired amount of.
The most popular material for the filling - concrete block. It is presented in the form of granules, who underwent calcination procedure in a special chamber. The porosity is very high, but the low weight. Fraction expanded clay should be no more 5 mm. If you take a large size, it will not be respected technology, but, Consequently, and dry strength markedly reduced screed. The best thing, to pellet size was completely identical. Otherwise, over time, fine granules may shift among large, and start "floating" floor.
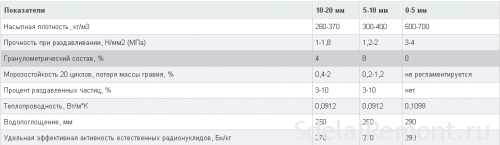
No impurities in Leca and should not be. If there is sand in its composition, then over time while walking the floors will creak. Control is better when buying loose granules. When performing work should adhere minimum layer of expanded clay, which should be 30-40 mm.
Vermiculite has a layered structure. In the manufacture of directly dry mixes for floors Device screeds, material itself is heated to a certain temperature. The result is such elements, that resemble worms, in the form of sticks. Its main advantage is that, it has a very light weight. Compared with the same expanded clay, by weight of the finished mixture is less than about 4 fold. The load on the existing overlap is reduced to a minimum. If you choose vermiculite, it should be exfoliated to a dry mix for a floor screed.
Perlite is a volcanic origin, which is also a material necessary for carrying out dry floor alignment. Here also applies firing process, the pellets were able to acquire all the possible qualities and properties. Moisture is practically reduced to zero. In addition to the perlite, It applies and sand on its basis.
Among proprietary reasons to backfill dry floor isolated Kompevit. But it has its advantages, which include low probability of marriage and falsification. This significantly distinguishes it, eg, of expanded clay, wherein in one bag may get caught granules of different size, with various impurities. Kompevit implemented, as a dry floor screed in bags. But it is worth noting, such that the basis material be expanded clay, with up to 0.4 cm. In this case, the density is much higher. This makes it possible to get such quality in service, as the absence of deformation and sagging embodiment finished floor.
If the surface under the floor is flat and does not require any intervention, it is possible to refuse filling. In this case, for floors mixture leaving aside, and in their place will be enough to put slabs of expanded polystyrene. She stacked close to the surface, and on top of them already carried out the installation of the floor covering. Composition dry floor screed in each situation will vary.
Consumables
Among these materials should include those components of the installation work, which are necessary in any case and at the same time, you can easily buy in the shop building products. This PVA glue or other adhesive possible, screws, screws, polyethylene film, used as a sound and heat insulating layer, edge band.
In each case, we can calculate the consumption of materials. When joining together the sheet material, per square meter have to spend each about 0.5 kg PVAc. I.e 1 kg would be enough for the whole room. May be sold and special tubes with adhesive. According to the number of packages will be difficult to determine, because they are all different, but a standard room 15-18 m2 will spend about 800-900 gram of material.
Edge band comes from the perimeter of the entire room, while subtracting doorways. But it is best to take in stock, especially if the line is not observed around the perimeter. Its thickness is in the standard 8-10 mm.
All sheets for dry screeds require the use of screws. approximately 6 pieces on each plate. In addition, it will have to spend in areas adjacent docking facilities. their length is 19 mm. These are the suitable for work on fastening sheets to dry floor screed. Longer options 30 mm needed in the double layer plates, when there is no communication under sub-floor.
Selection of the sheet material
Using dry screeds smooth floor obtained by observing technology. As the floor element can use various sheeting, which can be:
- The sheet of plasterboard.
- Plywood, able to withstand moisture.
- OSP (oriented plate) or DSP.
- gypsum sheets (GVL). It may further possess the property of resistance to moisture (GVLV).
Selection of a particular embodiment will depend on the humidity indoors, temperature changes.
If we take into account the most effective set of materials for dry floor OP 135 from the German manufacturer Knauf, then laid the basis of water-resistant gypsum board plate. True weight of the product has more to shortcomings. When the work is formed a lot of dust from the gypsum during cutting. It is certainly possible to stock the appropriate tools, as a jigsaw, equipped with a dust catcher. But it will require only additional cost. Buy it for one room or work in the apartment is not worth it.
When you select mixtures and materials for dry screed, It should be based on the recommendations of professionals, and acquire the best in the complex. This will avoid discrepancies in the quality of products, as well as in political parties. That will have a very flat floor, having high reliability and durability.