In modern construction field there are enough performance for floor screed. Among them is to provide a semi-dry screed, which is also used, to reduce the time of execution of all kinds of work on the project. Semi-dry screed can be performed not only using a special tool, but also independently. There are both advantages here, and disadvantages. The most important thing, that in the end it turns out really smooth surface, already used for floor covering.
notion
Semi-dry floor screed especially innovation is no different. It also prepared using sand and cement. true, very minimal amount of water application. No leak solution should not give. Sufficient to state, where from it is possible to make a lump. There can not even say that, that the device is a semi-dry screeds performed "pouring", but rather a conventional backfilling. In addition to this it is important to apply some of the subtleties and, make for a solid surface. We are talking about a semi-reinforcing ties, when it adopted as a material fiber of use. This product consists of polypropylene fibers.
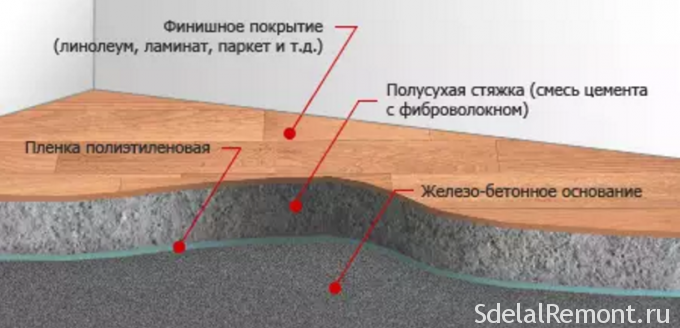
Depending on, which is necessary to obtain the result of the implementation of the floor screed, and distinguish certain technologies. Increasing the screed layer occurs when communications routing, however they were not. Much attention is paid to the floor with a large height difference.
Application area
As I mentioned earlier, technology is a semi-dry screeds finds its application in the case of shortening of the repair works. There is a great desire to quickly move into an apartment bought, when all kinds of works are carried out especially on their own. It is also necessary to carry and very thin slab. In this case, it is likely, cooked "wet" solution comes on downstream floors.
As a basis for semi-dry screed can act:
- Overlapping of wood, which are often found in old buildings.
- Concrete slab, used in modern construction.
- subgrade (gravel, sand, compacted material). With that you may encounter in a private home ownership, at the device basements, the organization of semi-dry screed on the ground floor.
Advantages and disadvantages
The type of material used for, as well as most of the installation technology, each embodiment tie has its positive and negative sides. The exception is not, and semi-dry screed. The device identifies the following semi-dry floors pros:
- Acceptable value of material required, as well as the payment of workers.
- Probability floor cod, appearance of any defect is reduced to zero. This result keeps its qualities and properties for a long time.
- It is not necessary to carry out additional measures for the implementation of floor leveling. After doing all types of jobs you can start laying the flooring.
- Characteristics of heat and sound insulation at times due to increased porosity available ready "rough" floor.
- No leaks during the installation work will not, since the use of water is minimized.
But it's only the main part of all those points, which recommends a semi-dry floor screed, even on its own. It is worth noting, that is not marked in any tangible negative qualities, If you work with your own hands. This indicates, that this method is very practical and the quality of the final result.
Significant areas is very costly to align the use of such technology. In addition to the purchase of material and equipment, You have to spend money on delivery to the job site, supply using specialized coiled tubing.
The disadvantages include the need for additional equipment for mixing. To prepare a semi-dry mixture will self-problematic and difficult. If there is no confidence in their own ability, it is best to contact the experts. Excess water can spoil even very expensive and high-quality cement brand. It is important here to perform a thorough rammer, to avoid cracking during operation. It is the latter gives rise to creak under the floor.
Variants of the dry screed
In order to realize a floor screed semidry device can be used completely different technology. For this reason, some isolated options for work for floor leveling:
- The substrate is not applicable, and coupling is carried out directly on prepared foundation of concrete.
- Using polyethylene substrate. Coupling with the walls and the base is not performed. In this way, obtained by the so-called "floating" embodiment screed.
- Laid on the surface of the screed is carried out on the device job membrane soundproofing.
- The substrate can be used for thermal insulation materials.
dry screed Technology
Each of these embodiments is able to perform certain functions, whichever, a used floor covering and what results should be available by the end of work. It is often performed semi-dry cement sand screed with fiberglass. It acts as a reinforcing base, which improves not only the quality of, but also the reliability of the whole structure.
Substrate preparation
floor operation time will depend, how well made all preparations. When cleaning substrates should be deleted all possible layers of old ties, until slabs. All garbage pickup, and small elements and dust are eliminated by using the construction of the vacuum cleaner. Thereafter, it is important to carry out the surface-coating. Even minor damage to a base are stripped using fine sandpaper. The grout would be necessary, to flatten large areas with defects.
When they spotted areas, where there was reason to delamination, using sandpaper carried out its cleanup. In a subsequent sealer will seal the damaged areas.
In determining the amount of solution for, It draws attention to the detailed measurements using a special tool, which may be a normal level. Better measurements are carried out using a laser leveling. The truth is not all of it will be in stock, that will appear during the work on its own.
Horizontal exhibited on the walls. Existing differences in height to be detected in time, to subsequently do not spend time on the purchase of an additional portion of material.
Lasers work is, that originally made its installation in the central part of the room, and the floor is screwed screw (length of at least 100 mm). It usually is put in the wrong place, where the laser beam intersects with rule, It is a marker of the mark. Similarly, the actions carried out and about the opposite wall. When the beam and the mark will not be the same, enough to screw or unscrew the screw to the extent necessary. The same is done and all the necessary facilities in the building. To the quality of work was high, along the walls screwed order 13-17 screws, and one of them is fixed in the central part of the room.
insulating layers
For waterproofing floor often use a film of polyethylene. the main thing, that its figures were within 100 m. If only pieces of film laid, then they should go to the overlap 15-20 see each other, as well as on the walls. layer of insulation is laid on top of it, running the sheet heater. It is important to choose a high-quality material, capable to serve for a long time and to transfer the entire surface of their quality.
The best option - use for thermal insulation boards made of extruded polystyrene foam. When the method is performed semi-dry screed with sufficient height, the suit and expanded clay. Moreover, its fraction should be at most 0.6 cm.
Insulation shall be all the walls in the room, available projections, column, possible elements architecture. For this optional damper tape, having the wrong adhesive base. semi-dry floor screed method includes lifting the tape, and other layers of insulation above the fill level of the future. Subsequently, it is all removed by the construction of the knife.
Fixing beacons
Important and crucial stage - the location of the beacons on the perimeter of the room. It will depend on him alignment semi-dry screeds. They needed not only to stop the rule, but the uniformity of the distribution of the finished solution throughout the room.
The requirements here are very high. For this reason, it is best to choose a T-shaped profile, and have an appropriate name - "the flashing" profiles. Choosing one of the walls as a guide, profiles are arranged parallel to it. The initial beacon is best to fix approximately 20-25 cm from the wall. Further the location of their implementation depends on the convenience of all subsequent works. The most important thing, the rule to be longer than the pitch beacons.
There is an option and cement lighthouses, are performed by screwing the screws into the base and fill them with cement mortar. But this is less common method, not possessing high efficiency.
The proportions of cement and sand
During the preparation of the solution for the semi-dry screeds should carefully follow the existing proportions. Materials needed:
- Recommended brand of cement - Portland cement M500 D0.
- coarse sand, Sift which follows or may be washed. No residue there should be no. Size of it should not exceed 25-30 mm and correspond to the first class.
- Water from wells, uncleaned. Otherwise, the water may be encountered, contaminated with various impurities and domestic waste water. About 15 liters for every 200 kg of mixture.
- Per square meter of the solution is acquired about 40 gram of fiberglass. It has a semi-dry screed with a slight weight fiberglass. Reinforcement semi floor screed in this case there is no need to perform.
- plasticizer. Liter of such material will be sufficient to 100 kg of cement.
Cement and sand are mixed in a proportion of 1 to 4 or 1 to 5 (it all depends on the strength of). Subsequently, the finished solution is poured water and proportionately fibrovolokno. As for moisture, preparing a mixture of the optimal - clenched, wherein the amount of moisture emerges slightly, and the lump itself remains intact.
To not bother and do not spend too much time, all available in the shop. For semi-dry screed solution presented in an assortment.
Carrying out installation work
Solution prepared in the distribution on the surface, should not stick to the tools, and smoothly distributed over the entire surface. In this case, should not appear no crackle semi tie. Mounting semi screed includes not only the distribution of the solution, but minor pridavlivaniya in the joints of insulation layers to the walls. Do not be amiss to ram it and throughout the perimeter, so as not to appear airbags.
It can be used and special equipment for the cooking mixture. But in this case, the entire surface must be simultaneously filled with solutions, and only then should start leveling. Flow semi floor screed will depend on the thickness of the floor surface under, as well as of the floor space. The thickness must be at least 30 mm. All installed beacons can be hidden under a semi-dry screed.
Zatirka
Once the tie around the perimeter of carefully rammed, it is possible to start leveling. Edges of rules rests on the exposed lighthouses and gradually shifted to the opposite side. This further indicates the places, where there is little or vice versa to pour a lot of solution. Using a trowel or trowel, Lots are in the optimum position.
It refers to the final stage semi-floating screed. The best option - the use of specialized equipment, which is a grinder disk. Trowel strap suitable for work with his own hands. Technology laying semi-dry floor screed provides for implementation of a circular motion for grouting.
meticulous care
The process of semi-dry floor screed does not take much time. But it is necessary to create conditions, that the resulting solution could solidify on the surface. The most commonly used plastic film, he served. It creates optimum temperature around the perimeter. Preliminary results will be evident later 10-12 hours. If there are small voids, they can be filled with semi-liquid cement solution. An alternative to acts and constant irrigation water surface.
Proceed to the deck floor covering can only after 94 hours after, as polyethylene surface will be removed in the "rough" floor. But even during this time, it is necessary to monitor the condition of paintings.