- What is the difference between roller and trolley wheel?
- How to determine the load capacity of your industrial casters?
- Why add buffer load capacity for industrial rollers?
- What factors determine the load capacity of industrial rollers?
- Wheel diameter
- Roller tread width
- Roller tread profile
- Soft industrial rollers vs hard industrial rollers
- Performance
- Gender protection
- Floor Obstacles and Work Environment
- Cost analysis
- Varieties of wheels for the right choice
- swivel castors
- Threaded rollers
- Rollers with rod
- Nylon wheels
- Rubber wheels for rokhli
- iron rollers
- Polyolefin
Trolley wheels come in two basic shapes: solid construction or pneumatic (also called hub and tire). Both shapes offer benefits for a range of applications and are available in a variety of wear-resistant materials, such as rubber, polyurethane (PUR), polyamide and polypropylene. Polyurethane wheels are widely used due to their very high load capacity and resistance to abrasion and tearing. They are chemically resistant, making them suitable for use in hazardous environments. Solid rubber wheels provide a smooth ride and quiet operation combined with excellent aging resistance.
There is a wide range of industrial rollers, each one has a different load capacity. This carrying capacity is a measure of, how much weight the wheel can support when rolling. If you overload the rollers , this can lead to premature failure of the industrial product or damage to the floor. Therefore, it is important to choose the right wheels for roaches.
What is the difference between roller and trolley wheel?
Although casters and wheels are often used together, they are two separate items. The roller is the body shape, often with an attached wheel, which allows wheels and objects to turn and rotate. Trolley wheels are ideal for applications, requiring a simple, but effective movement, especially when transporting heavy loads.
Wheel hubs and tires are elastic, which is especially suitable for high loads and carrying capacities. They provide a soft ride, facilitating manual transportation of goods. Being puncture resistant, they are ideal for heavy-duty applications and work well on difficult, rough or uneven surfaces, such as grass and gravel. Closed cell tire does not absorb water, does not freeze or crack, making it ideal for extreme conditions without the need to re-inflate
How to determine the load capacity of your industrial casters?
When purchasing industrial strength casters, the exact load capacity of the caster should be studied and documented for future use..
There are three standard load ratings for industrial casters:
- Lightweight rollers can withstand loads up to 25kg.
- Industrial rollers begin to withstand loads up to 200 kg.
- Heavy industrial rollers are required for loads over 2000 kg.
The individual load capacity of your rollers is not, what needs to be calculated; you need to determine the maximum load, which you want to move, add it to the weight of the cart or equipment, moving, and then add 33 percent over this for the safety buffer.
After that, how did you determine your total weight, divide it by the number of clips, that will be on your equipment, to determine the minimum load capacity for each roller, which you will need to purchase.
If you want to move 2000 kg. in na 100 kg trolley with four wheels, you will need four rollers, who can endure 700 kg each, and if there is no video, which can withstand exactly the same figure, you will need to buy up to the next largest roller load capacity.
Why add buffer load capacity for industrial rollers?
Adding a safety buffer in size 33% to the load capacity of your industrial rollers may incur additional costs, especially with relatively large rounding.
One problem with determining the load capacity of a roller is that, that it is maximum under ideal conditions. Intermittent operation or load on smooth floors at less than 3 km per hour - ideal conditions for industrial crumbling.
If your environment and use of rollers is not ideal, safety buffer is an inexpensive way to keep workers and products safe.
What factors determine the load capacity of industrial rollers?
The load capacity of industrial rollers can be determined by many factors.; Understanding, what and how each component determines the load capacity, help you choose the right video for your job.
Below you will see, that each factor in itself can have a significant impact on the carrying capacity, which means, that you can consider your requirements and find the right roller, which will give you the most benefit, and not just choose one factor to increase the load capacity.
Wheel diameter
The diameter of the caster wheel is an important factor in the load capacity of the caster wheel.. The larger the diameter of the caster wheel, the more weight the roller can bear in general.
for example, if all others are the same for a roller of the same brand, load capacity nominally increases with roller diameter.
- 6 -inch heavy duty casters have load capacity 900 kg.
- The load capacity of 8" heavy duty casters is 1000 kg.
- The load capacity of 10" heavy duty casters is 1300 kg.
- The load capacity of 12" heavy duty wheels is 1500 kg.
Usually, increase in the diameter of the caster wheel by 2 inch leads to a permanent increase in additional load capacity. You also get bigger diameter wheels, easier maneuverability and the ability to handle uneven surfaces more easily.
However, you should check specific products, as there may be other differences, affecting the carrying capacity.
Roller tread width
Wide tread caster has a large load capacity, the thinner gauge. If you take heavy-duty rollers with a 3″ gauge and reduce it to 2.5″, load capacity will decrease.
- The load capacity of 6" heavy duty wheels with 2.5" tread is 680.
- The load capacity of 8" heavy duty wheels with 2.5" tread is 900 kg.
- The load capacity of 10" heavy casters with 2.5" tread is 1000 kg.
- The load capacity of 12" heavy duty wheels with 2.5" tread is 1500 kg.
How view, even a small reduction in track width has a significant effect on wheel load capacity. It also circumvents height restrictions by increasing roller tread., not roller diameter, to increase the load capacity.
Roller tread profile
Roller tread profile can affect load capacity; You can choose between a rounded or flat tread profile.. Rollers with a flat tread profile last longer and carry higher load capacities by distributing the load over a larger surface.
On the other hand, rollers with rounded tread profiles have excellent maneuverability and roll much easier. In this way, depending on your future budget and maneuverability requirements, you will need to select the best roller tread profile for your requirements.
for example, when using the same industrial strength rollers, the load capacity differs significantly between flat and rounded tread:
The load capacity of 6-inch heavy-duty wheels with rounded tread profiles is 200 kg.
The load capacity of 6" heavy castors with a traditional flat profile is 270 kg.
Another significant difference in load capacity with rollers of the same type.
Soft industrial rollers vs hard industrial rollers
Soft rollers, usually, quieter and more agile, if they are made of such materials, like polyurethane, but have a much lower load capacity compared to solid rollers, made from such materials., like steel.
Most manufacturers will use hard material for extreme industrial strength rollers and soft roller materials for lighter and more delicate conditions..
Performance
On the productivity of equipment and people, who use it, wheels and rollers affect. Choosing the right wheel or roller ensures maximum performance, reduces long-term costs and maximizes return on investment.
The basis of any rolling stock is its wheels.. Bearings drive the wheels, affecting performance. Poor quality tires and bearings do not provide profitable operation, especially when they are geared towards heavier loads or booster work. Their use requires expensive maintenance, broken equipment and a large amount of labor to move, when power is not supplied..
When choosing a wheel or castor, keep the safety and well-being of your employees in mind. A person has to move equipment in a manual application.
The larger the wheel diameter, the easier it is to roll. Proper tire construction and composition also affect performance..
Ergonomic casters and wheels reduce the likelihood of work-related injuries. One example is swivel casters with precision swivel bearings. This feature allows the swivel caster to turn more easily under load., Reduces starting effort and fatigue, and also provides more stable performance. When you consider safety and ergonomics, you save time, lost due to accidents.
Gender protection
Repairing or replacing floors is an expensive pleasure.. Bad floors harm equipment on casters, reduce productivity and endanger personnel. Choosing the most suitable floor protection wheel for your application will protect good floors and reduce the wear rate of floors, which have already fallen into disrepair. Only wheels with soft rubber tread protect floor and load. These include ordinary cast wheels, pneumatic and gray rubber. A common mistake is to think, that polyurethane wheels protect the floor.
Although under load they are capable of some tire deflection., the actual "flex" of the tires is rarely noticeable. Most polyurethane wheels have a hardness, comparable to "hard tread" wheels (phenolic, polyolefin, ebonite), but not as noisy. Hard 'jackhammer' tread wheels will erode most floors over time. However, even metal wheels fulfill an important need, when operating conditions or power do not allow the use of anything else.
Choices should never be made based on opportunity alone.. Load ratings are offered as an indication of how, that the wheel or roller will carry without failure. They are not absolute., but rather dependent on usage and maintenance. The load ratings shown do not include shock loads., overload, mishandling, obstacles or bad floors. Proper maintenance requires, that all bearings are regularly lubricated, and all bolts and nuts were tightened. Over temperature conditions, dirt or other contaminants reduce performance and minimize performance. Temperature range, specified for wheels in this catalog, match wheel material range. Operation near either end of the temperature range may require a significant reduction in performance or render the wheel unusable..
Floor Obstacles and Work Environment
Sometimes obstacles have to be endured. Examples may include expansion joints, which are not equal, guides, docking slabs or brick floors. There may not be a perfect solution. but, usually, elastic wheels overcome obstacles on the floor better, than hard tread wheels. Obstacles require the choice of larger wheels and stronger rollers, than would be required to apply, if the floor was smooth. Metal chips can get stuck in rubber and polyurethane tires. Steel plates can cut elastic tires, as well as chip or break hard-tread wheels.
Always clear floors of debris. Harmful substances or chemicals may require the use of special wheels or bearings. Binder, which holds rubber and polyurethane tires on their metal centers, can be damaged by exposure to certain chemicals, blows, overload and heat accumulation. Stainless steel rollers are made of stainless steel 304, which is rust resistant. Under some severe conditions over time, stainless steel 304 may rust.
Cost analysis
Too often the purchase of wheels and castors is based on criteria, far from the main goal: “Will they move the load easily and smoothly?» Equipment Part, purchased for carrying and moving cargo by weight 1000 kg is expensive, if it's loaded 200 kg. Most people only load equipment up to weight, which they can move easily and without injury. Equipment, which requires two people to move, when one is enough, is also an expensive unit, regardless of acquisition cost.
Rollers and wheels of old design are usually made at a price without regard to their investment value for profitable operation and productivity payback. Our products are competitively priced, but not limited to the price tag. Initial cost is a factor, influencing the purchase decision, but that's just one factor.
Consider doing a cost analysis, it may reveal some other factors, noteworthy. Product value assessment. A person must push or pull the roller equipment. Rolling ease and wheel life are two important elements of efficient and economical manual control.. Sometimes a particular roller or wheel may not be the cheapest choice., if you are only looking at the initial acquisition cost. but, if the roller or wheel is suitable for the specific application, the cost will be commensurate with the cost and payback.
Ask yourself, the extent to which the roller or wheel requires maintenance? The cost of acquiring a product should be compared with the cost of maintaining it in working order.. Bearings and their maintenance, usually, are the biggest maintenance factor. The cost of systematic lubrication and replacement can lead to loss of profit; if one is neglected, the other increases.
Will the roller or wheel work reliably? With a lighter rolling wheel and easier turning, employees are less tired, fewer accidents and increased productivity.
When purchasing industrial wheels for raking, There are two main types to keep in mind.: swivel castors and rigid castors. Each type of cluster has its pros and cons..
And fixed, and swivel castors have bearings in the wheel, which allow them to move the wheel back and forth along the way. This movement can be used, to turn a wheel or apply force to a load, to move it up or down. On stationary rollers, this force is generated by the bearing., installed inside the roller. In a swivel castor, the ball bearing is mounted outside the wheel in the "race".
Varieties of wheels for the right choice
There are many differences between rigid and swivel casters. . One side, both are very easy to move, despite, that they are heavy, but the rigid caster can only move in a straight line. Besides, wheels on a fixed roller cannot turn in the direction, wheel parallel path. To their credit, but, they have locking mechanisms, which make them very safe. so here, in this case, rigid rollers have a slight advantage over swivels. The swivel roller is, what you need, if you want to move something with a heavy load.
swivel castors
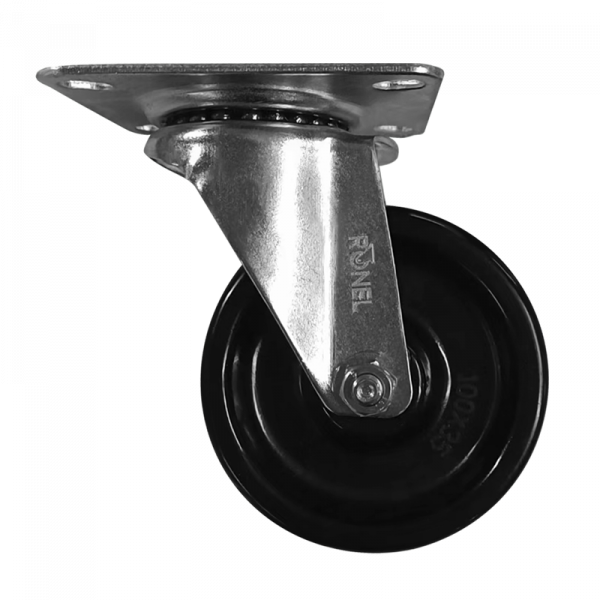
There are a few moments, to think about, choosing between rigid roller and swivel roller:
- What are the dimensions of your equipment?
- You only need to drive in a straight line.?
- How much does it weigh?
- Is there a way to block?
- How wide is the technique and how big is it?
- As already mentioned, swivel casters make it easy to move things.
Because of this people, who need rollers for industrial or commercial use, may find them easier to use. But not all needs are the same. Each of these designs are easy to wear in different ways. Choosing wheels for rokhli, you have to make sure, that they will fit in the space you have and that they are quite versatile, to meet your specific needs.
Threaded rollers
There are two ways to install a threaded rod roller: or you need to install a threaded insert, so that the threaded roller can be screwed into the insert, or you can cut a hole in the hardware .
If you can get to the other side, you can also drill something. You can then put the lock washer and lock nut on the stem threaded wheel and tighten them with a wrench. It's a good choice, if your base is not too thick and you don't have room to mount a threaded insert for heavy rollers.
Tube or tube frames are one of the most common ways to use threaded rod rollers.. The lock nut makes it very useful, because you don't need to set it to any insert. Instead, you can just drill a hole in there., where do you need it.
Rollers with rod
Stem roller is a great choice, if you need videos, which are easy to install and replace. However, it comes in different types., depending on your needs and, how do you want to use it. The rollers on the rod have a long rod, which can be inserted into the table, a chair or any other item with enough space, to insert a hole for the rod.
There are many types of rod rollers: threaded rollers, rods with gripping ring, neck rods, expanding rubber rods, as well as square and round rods with transverse holes for wire shelving.
Ring rod rollers can be used for a variety of things, they are mainly used for chairs and furniture. You should use rollers with ring rod, when you are not going to lift furniture or other equipment, and gravity will hold everything in place. If you apply force to the wheel, it might fall out of the nest.
If you cannot reach the back of furniture or equipment, where do you want to install the rollers, eg, on long wooden legs or thick plastic, the best choice would be rollers with a ring handle.
Handle roller inserts can be made from almost any material, eg, wood, welded inserts, PVC, metal or plastic. If you need a heavy duty roller, but you can't reach the back, to put on the lock nut, a roller with a stem with a handle is best.
Nylon wheels
Nylon wheels are made of durable nylon material. Black nylon wheels reinforced with fiberglass to increase load capacity and reduce rolling friction. Some nylon wheels can be supplied with either stainless steel bearings, or with a smooth bore for applications, in which the wheels are exposed:
- Sweep
- Steam cleaning
- Salt
- chemicals
- organic solvents
- Oil
- grease
Despite, these wheels are very light, they can carry the same load, like most metal wheels, and will not slide on the surface. Nylon wheels are best for use in wet and corrosive environments, where chemical resistance and higher load capacities are required.
Not recommended, if your solution contains more than 10% acid.
Rubber wheels for rokhli
Tires on rubber rollers are made of gray thermoplastic rubber, which has been pressed by injection molding, and then mechanically bonded to the polyolefin (industrial plastics) center. They are often used on equipment in pharmaceutical laboratories., hospitals, catering services and other institutions. These rollers are softer, than polyurethane, and provide a quieter ride. They can be used in industrial environments, not related to punches, overloads, mistreatment, obstacles, poor floors or warehouse (permanent) loads. RH wheels can fit a little more, than our other gray soft rubber wheels.
No other wheel material performs better, than soft rubber, when it comes to his movement. Non-marking soft gray rubber wheels, silent, absorb shock (which protects the cargo and extends the life of the equipment), can roll small objects, protect expensive floors and reduce vibration. They are not perfect, because they are not easy to roll, when they are full.
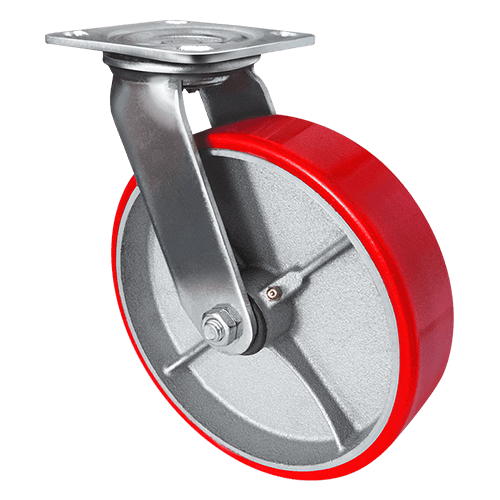
If you want to move things by hand with these gray soft rubber wheels, halve the rated capacity and choose the largest diameter wheels, whatever you can. You should not leave these casters loaded for long periods of time., because tires can "sit down" or get a puncture. Almost any dry factory floor can be used with them.. Glue, which attaches the rubber tire to the polyolefin center, may collapse, if it is exposed to certain chemicals, by a blow, overload or heat.
iron rollers
These stamped iron wheels are cheaper, than forged or forged steel wheels. They are useful for transporting light loads on wooden blocks or smooth hardened concrete in cases, when they won't be misused. On concrete floors, which have not been processed, they tend to damage the floor quickly. Forged wheels, forged or machined steel are the only, which we recommend for applications, which can be rough for the wheels. Abuse includes things like this, like impact loads, pounding, bad floors or obstacles on the floor, overloading and use of mechanically driven equipment.
When the load is too great for the wheels, protecting the floor, or when operating conditions are unusually harsh, rollers made of durable steel or forged steel will do the job. Most of the time the user will not think of floor wear as a big issue in these applications due to the work being done.. Most factory shops cannot handle forged steel casters, so they are usually used on steel plates, in channels or as wheels with V-grooves.
Forged and forged steel wheels have high ductility and tensile strength, so they can withstand bumps and bumps, without breaking. In normal use, these one-piece (without spokes) wheels cannot be broken. Their carrying capacity is limited only by, how much capacity can they hold.
Videos, made from solid hot rolled steel bars, called "treated steel". They handle shock loads well and have a high capacity., durability and performance. You can choose between Bronze Inner Diameter Bearing 3/4 inch or roller bearing with inner diameter 3/4 inch. Both wheels come with a wrench sleeve with an inside diameter 1/2 inch, so that they can be put on the roller axis 1/2 inch.
Depending on usage, these steel wheels can withstand temperatures up to 700°F.. Steel roller bearings and wrench bushings can start annealing at temperatures above 400°F, that remain unchanged for a long time. For Applications, where the temperature is higher 400 ° F, you are welcome, contact our engineering department.
Polyolefin
Polyolefin wheels are made by injecting a mixture of thermoplastic polymers into a mold for a durable hygienic construction, which is a whole. Like nylon wheels, these polyolefin wheels are particularly suitable for wet and corrosive conditions. They are very resistant to most liquids., which you may encounter. Except for our heavy duty polyolefin wheels , polyolefin wheels do not have such a high load capacity and can only be used in a smaller temperature range, than nylon wheels (prefix RK). Polyolefin wheels can break, if stored in a cool and dry place, e.g. in a refrigerator. They cannot be used in the freezer or washing machine..
Heavy duty polyolefin rollers (RK prefix in part number) reinforced with fiberglass to increase their load capacity. The load capacity of these extra heavy polyolefin wheels is the same, like nylon wheels. They also perform well in wet and corrosive environments.. Heavy duty polyolefin wheels come standard with precision sealed stainless steel ball bearings (PS) and precision sealed stainless steel ball bearings (SPS).